With around 13 percent of the global cereals production in 2013, the European Union (EU) is also one of the largest straw producers. Most of this straw is still unused, but its energy potential is extremely important. The biogas plant in Bulgaria is a good example of its implementation.
The annual cereal production results in enormous amounts of straw as each ha of cereal generates between 2 and 3 tonnes of straw. In fact, most of the straw has no direct application but is directly ploughed under.
According to Netherlands-based biogas technology developers HoSt, one tonne of digested straw can yield 300 – 400 Nm3 of biogas which, if upgraded is about 180 – 250 Nm3 biomethane or fossil gas equivalent.
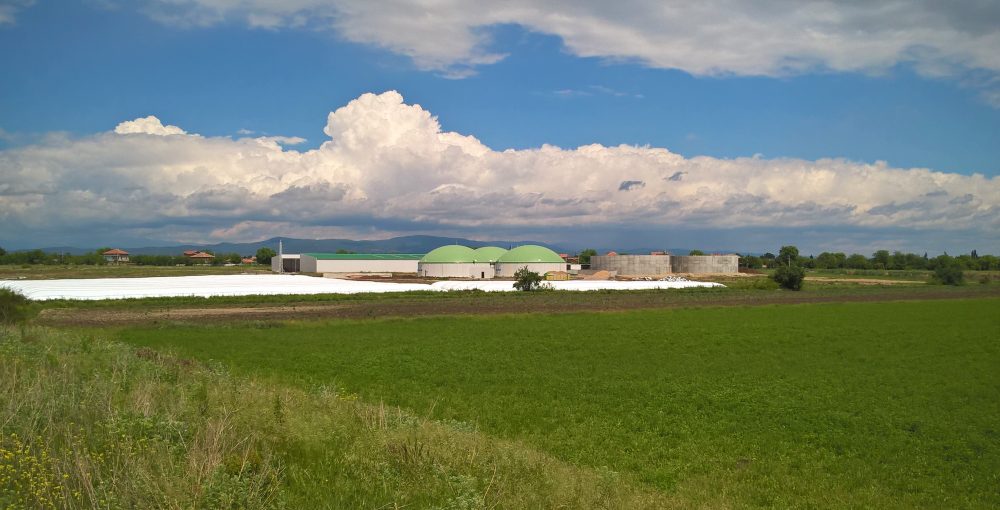
The energy use of straw
There are four energy conversion pathways for straw:
- fermentation for liquid biofuels;
- anaerobic digestion for biogas;
- combustion for heat and/or power;
- gasification for syngas.
The biogas production is becoming more and more relevant during the process of the abandonment of Russian natural gas and the introduction the policy of combating climate change.
Currently, we can build anaerobic digestion plants using only agricultural residues as input streams, without the need for dedicated energy crops.
Difficulties with using straw as an energy source
- A straw is a “difficult” material because it is a light, dry material.
- Using a straw will also increase the solid content in the digester, which calls for special mixers.
- To digest large amounts of straw, you need special feeding systems, because of the large volumes.
- You need special pre-treatment and the conversion process is relatively slow, especially in the beginning.
It is interesting that HoSt has conducted an extensive research programme in association with the Technical University of Münster in Germany on the preparation of straw to increase conversion. Some of the research topics included making powder, hammering, thermal treatment at medium temperatures together with acid or high-temperature treatment, and enzymes.
The high thermal treatment gave the highest gas production per tonne of straw, but needs a large amount of steam, more than a gas engine can supply. It is also an expensive system that is difficult to make economically feasible.
Therefore HoSt is focusing on low-temperature pre-treatment, where hammering is one of the best options.
Biogas plant in Bulgaria
The company operates a 1.5 MW manure-based biogas plant in Bulgaria with a dedicated straw input system. It was the first biogas plant in which large amounts of straw are fed. The 1.5 MWe capacity plant uses around 50 000 tonnes per annum of cow slurry co-digested with maize silage and straw.
The Chernozemen facility consists of a dedicated solid feeding system, a liquid input system consisting of a pump and cutter, two 2 174 m3 digester tanks, a single 2 174 m3 post-digester tank, a separator system, after-storage tanks, and a building with a control and heating room, a 1.5 MWe gen-set and a room for the operator.
One of the striking features is the dedicated straw input system. Straw bales are placed on a large straw conveyor that can handle straw bales and feeds the bales to a bale breaker. Here the first initial size reduction takes place before a hammer mill. The hammer mill is sufficient to mill the straw enough to break its tubular structure to prevent floatation. Tests were conducted with different sieve sizes to find the optimal particle size for the digestion process.
Apart from the feeding system, the digester tanks are optimized for the digestion of straw. A special paddle mixing technology combined with propeller mixers ensures that no floating layers are formed.
Further nutrient capture
Another advantage is that nutrients, such as nitrogen (N), potassium (K), and phosphorus (P) are made available for use as fertilizer along with the organic matter in the digestate.
The additional biomass not only leads to increased biogas production but also the available organics on the land increase. Moreover, the winter cover crop reduces the risk of mineral and nutrient leaching.